Case Study: Successful Collaborative Solutions in Injectable Manufacturing
Introduction to Collaborative Solutions in Injectable Manufacturing
In the rapidly evolving pharmaceutical industry, the demand for injectable drugs is surging. As a result, manufacturers are constantly seeking innovative solutions to boost efficiency and product quality. One of the most effective strategies is collaboration, where different stakeholders come together to enhance the manufacturing process. This case study explores how collaborative solutions have led to successful outcomes in injectable manufacturing.
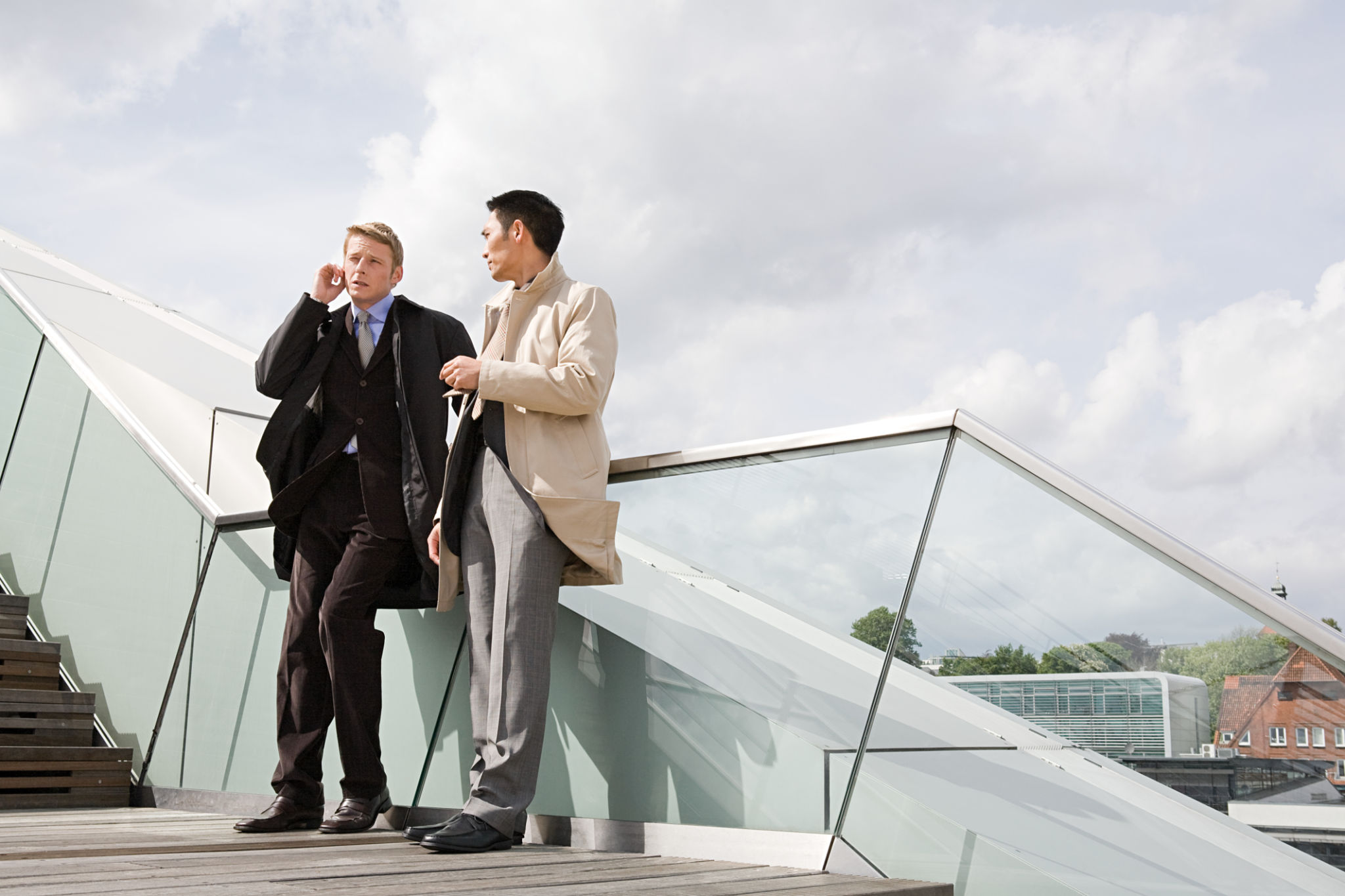
The Need for Collaboration
Manufacturing injectable drugs involves complex processes that require precision and high standards of quality. With stringent regulatory requirements and the need for cutting-edge technology, manufacturers often encounter challenges that cannot be tackled single-handedly. Collaboration allows companies to leverage shared expertise, resources, and technology to overcome these hurdles.
Key Stakeholders in Collaborative Initiatives
Successful collaborations in injectable manufacturing typically involve a variety of stakeholders, including:
- Pharmaceutical Companies: These companies bring their expertise in drug formulation and regulatory compliance.
- Contract Manufacturing Organizations (CMOs): CMOs offer specialized manufacturing capabilities and facilities.
- Technology Providers: These entities supply advanced equipment and software solutions.
- Regulatory Bodies: Their input ensures that all processes meet the necessary health and safety standards.
Case Study: A Collaborative Success Story
An exemplary instance of successful collaboration involved a leading pharmaceutical company partnering with a cutting-edge CMO and a technology provider. The pharmaceutical company required a more efficient production line for a new injectable drug. By joining forces, they were able to significantly reduce production time and improve yield.
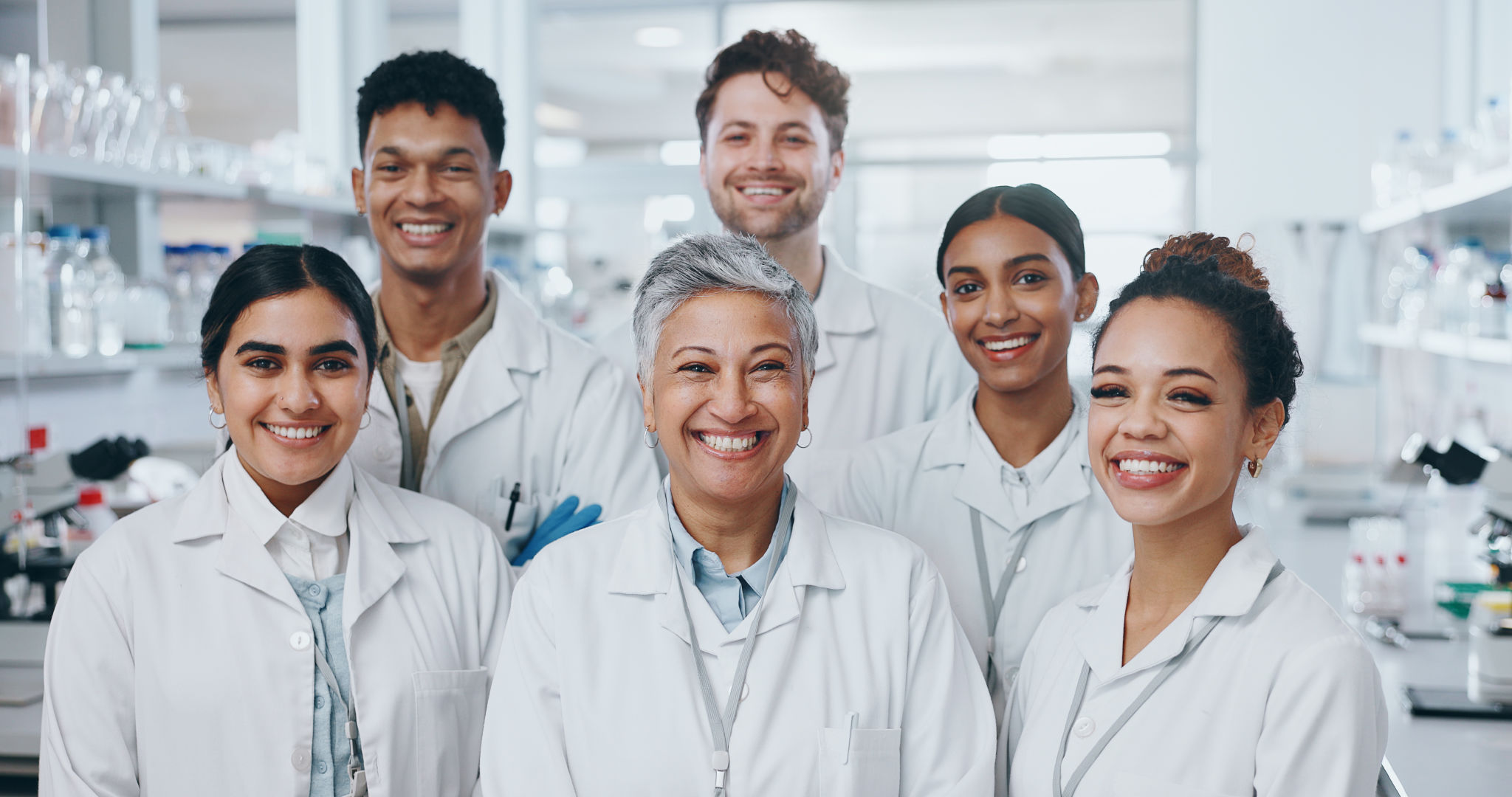
The Role of Technology in Collaboration
Technology played a pivotal role in this collaborative effort. The technology provider introduced an innovative automation system that streamlined operations, minimized human error, and enhanced precision. This system enabled real-time monitoring and data collection, facilitating proactive adjustments to the manufacturing process.
Outcomes and Benefits
The collaboration resulted in several key benefits:
- Increased Efficiency: Production time was reduced by 30%, allowing for quicker market entry.
- Enhanced Quality: The precision of the automated system improved product consistency and compliance with regulatory standards.
- Cost Savings: The reduction in manual labor and process optimization led to significant cost reductions.

Challenges and Lessons Learned
While the collaboration was successful, it was not without challenges. Coordinating between multiple stakeholders required effective communication and project management. One key lesson was the importance of establishing clear objectives and roles from the outset to ensure smooth collaboration.
Conclusion: The Future of Collaboration in Injectable Manufacturing
The case study highlights the immense potential of collaborative solutions in transforming injectable manufacturing. As the industry continues to evolve, such collaborations will be crucial in driving innovation and maintaining competitive advantage. By working together, stakeholders can achieve outcomes that are both efficient and beneficial to the end consumers, ultimately leading to better healthcare solutions globally.